Enhancing Productivity and Top Quality Through Modern Steel Stamping Techniques
As the needs for accuracy and effectiveness continue to escalate, the integration of automation and digital devices into the metal marking process has actually become critical. By discovering the detailed interaction in between technology, automation, and precision in metal marking, a path in the direction of exceptional efficiency and top quality guarantee unfolds.
Advantages of Modern Metal Stamping
Modern metal stamping offers many advantages in regards to effectiveness, accuracy, and cost-effectiveness in the manufacturing market. One of the key benefits of contemporary steel marking is its capability to successfully generate high volumes of complex metal get rid of consistent top quality. This procedure eliminates the demand for numerous procedures as it can execute different tasks such as blanking, puncturing, creating, and pulling in a single procedure.
Moreover, contemporary steel stamping makes it possible for makers to attain tight resistances and precise specs, making sure that each part meets the needed requirements. This high level of precision results in marginal product waste, minimized rework, and general improved product quality.
Additionally, modern metal stamping is an economical manufacturing approach. In significance, contemporary metal marking offers an affordable edge to producers looking to improve efficiency and quality in their procedures.
Advanced Technologies in Metal Stamping
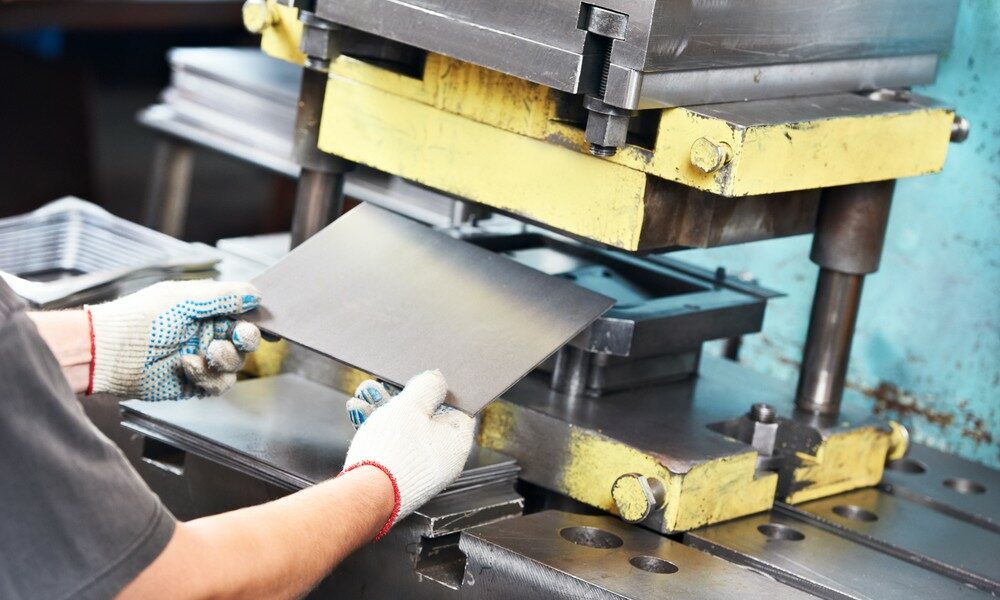
One more essential modern technology revolutionizing steel stamping is the use of servo presses. Unlike typical mechanical presses, servo presses use greater control over the rate and force used throughout the stamping procedure. This control not only boosts the high quality of the stamped parts yet likewise reduces product waste and energy intake.
Additionally, advancements in simulation software program have enabled makers to practically examine and enhance the marking process prior to physical production starts. This virtual prototyping assists identify prospective concerns early, leading to cost financial savings and faster time-to-market for new items. Overall, these sophisticated modern technologies in metal marking are driving extraordinary levels of performance and quality in the market.
Improving Performance Through Automation
The combination of automated systems has actually considerably improved the performance of metal stamping procedures. Automation in steel marking operations uses a myriad of advantages, consisting of enhanced manufacturing prices, boosted accuracy, and decreased labor expenses. By making use of robotic arms and computer-controlled machinery, tasks that were formerly taxing and vulnerable to errors can now be performed quickly and with impressive accuracy.
Automated systems have the capability to over at this website deal with repeated jobs with uniformity, causing greater performance degrees and reduced cycle times. This increased effectiveness not only causes set you back financial savings yet additionally makes certain a more streamlined and dependable production process. Furthermore, automation enables real-time tracking and information collection, allowing makers to recognize and attend to concerns without delay, more enhancing the general effectiveness of metal stamping operations.
Moreover, automation advertises a more secure working setting by minimizing the requirement for hands-on intervention in hazardous jobs. By passing on these duties to automated systems, employees can focus on more complex and value-added tasks, adding to a more reliable and efficient process in the metal marking market.
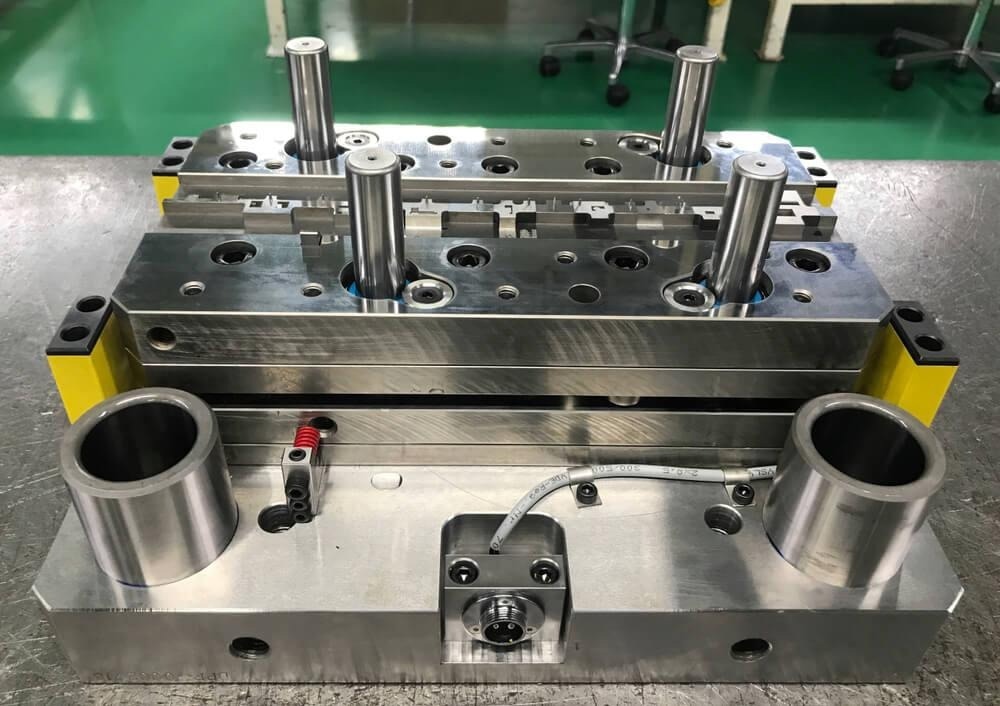
Top Quality Control Procedures in Stamping
Implementing rigorous quality assurance procedures is critical in ensuring the accuracy and consistency of steel stamping processes. By developing robust quality assurance procedures, producers can recognize and remedy any inconsistencies or problems in the stamped parts, eventually enhancing item quality and consumer fulfillment. Among the main quality assurance procedures in metal stamping is conducting routine inspections throughout the manufacturing cycle. These inspections include checking the dimensions, surface area finish, and total integrity of the stamped elements to validate compliance with the specific requirements.
Additionally, executing innovative modern technologies such as automated vision systems can even more enhance the quality assurance procedure by enabling real-time monitoring and Visit This Link detection of any type of abnormalities throughout manufacturing. These systems utilize video cameras and computer system formulas to evaluate components with high accuracy and accuracy, reducing the threat of defects getting away into the end product.
In addition, developing a thorough documents system that records quality assurance data and assessment results is essential for tracking efficiency fads and promoting continuous enhancement initiatives. By evaluating this data, suppliers can recognize possible locations for optimization and carry out restorative actions to enhance the overall quality of their stamped items.
Enhancing Accuracy With Digital Devices
Utilizing electronic tools can dramatically boost the accuracy of metal stamping processes, changing the way suppliers accomplish accuracy in their manufacturing. Digital tools such as computer-aided design (CAD) software permit the development of elaborate marking designs with unbelievably specific dimensions. By inputting in-depth specifications right into the software application, suppliers can get redirected here make sure that each stamped piece fulfills precise dimensional requirements, minimizing mistakes and waste in the production procedure.
Furthermore, the assimilation of sensors and real-time monitoring systems in stamping tools enables makers to very closely monitor the marking procedure and make prompt adjustments to make certain specific outcomes. These electronic devices give important data on variables such as pressure, rate, and positioning, permitting fast recognition and improvement of any type of deviations from the preferred specs.
Final Thought
To conclude, modern metal marking approaches use various advantages for enhancing productivity and top quality in producing procedures. By utilizing innovative modern technologies, automation, quality assurance steps, and digital devices, firms can enhance effectiveness, accuracy, and general efficiency. These technologies in metal marking not just improve manufacturing procedures yet likewise guarantee regular and high-quality results. Welcoming these contemporary methods can result in significant advancements in the manufacturing industry.